Logistic
AMYR Trading Company INC offers the services required to trade and distribute asphalt and other oil refined commodities for industrial and construction application.
In the specific area of asphalt, AMYR’s line of specialization, give our customers special attention to the management of asphalt transportation and storage, as well as the management and operational procedures for loading, unloading and final delivery of the product
Asphalt Storage
Due to its high viscosity, asphalt is stored in vertical cylindrical tanks with a fixed roof, according to API 650 or BS 2654, made of carbon steel plates, welded and heating systems. The higher the temperature, the lower the viscosity and the easier it is to transport from tank to tank and from tank to ship or barge. To keep the asphalt at the required temperature of 140°C, the tanks are equipped with steam or thermal oil coils, which are located at the bottom of the tank. In addition, the tanks have external insulation made of fiberglass 0.1 meters thick, covered with aluminum plates used as a barrier. For access to the tank roof and to control the volume of the product and other operations, a helical ladder is considered. Heating systems using steam coils have the disadvantage that they may present a water leak through a coil that could have corroded, resulting in the violent vaporization of water.
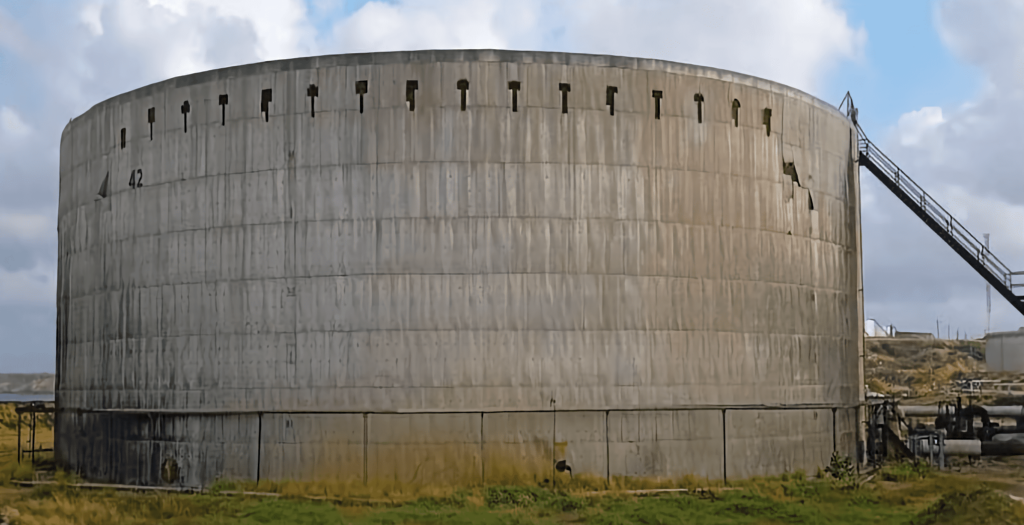
The following figure shows a schematic of the steam coil in an asphalt storage tank. The steam comes from a 10 bar superheated steam boiler at a temperature of about 180°C, in order to maintain the asphalt at a temperature above 130°C.
Asphalt tank´s general construction characteristics:
Asphalt storage tanks are built with sheets of carbon steel or sheets of alloy steel, of various sizes and capacities, with vertical cylindrical walls, with a flat bottom and a fixed conical roof (cover with the shape and surface of a straight cone) supported on a structure or frame that rests on the tank wall and is in turn supported by internal columns (according to API 650 code). In its construction, riveted or welded horizontal rings are used one above the other, where the last one is attached to the ceiling. They are placed as bases on the roof, bent angles of structural steel with the radius of the shell to join the shell with the roof and the bottom where they are riveted strongly, the joints are carefully closed to prevent the escape of liquids.
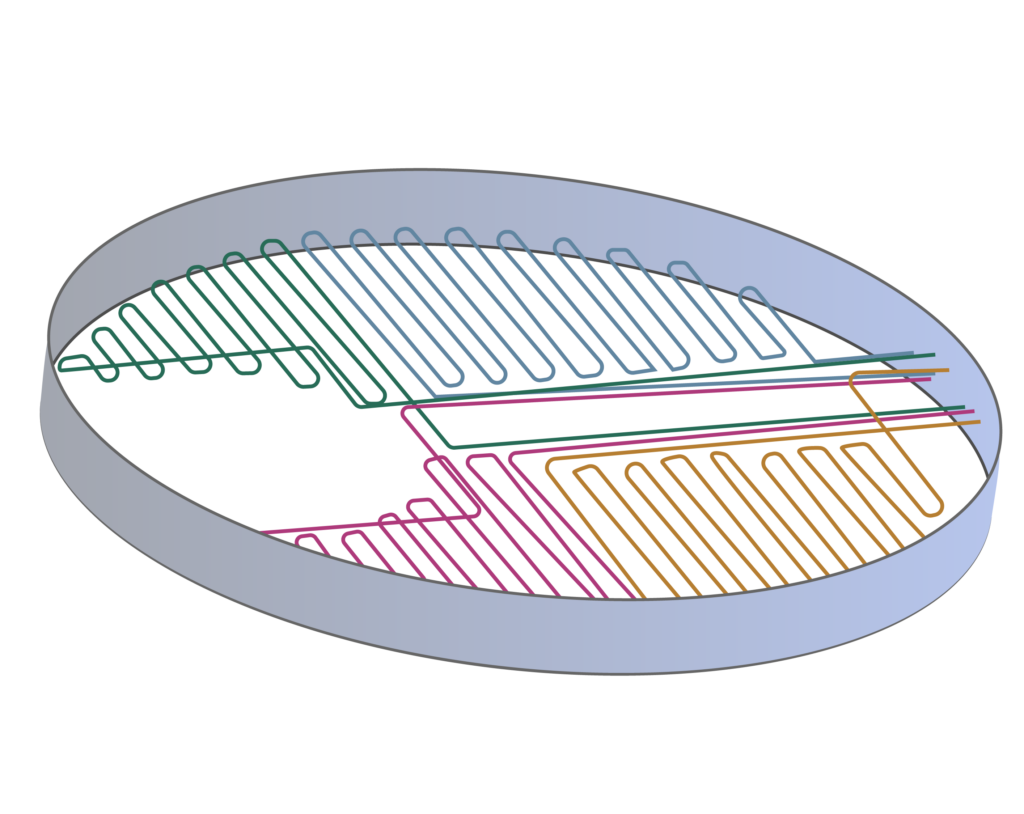
Structure of the storage tank for asphalt.
Additionally, these tanks are provided with external thermal insulation of low thermal conductivity, made up of a layer of insulating material, which can be made of fiber or mineral wool, calcium silicate, expanded perlite, cellular glass or hydraulic cement) fixed with plates or welded sheets, with adjustment bands, stainless steel wire for ties, stainless steel expansion springs, self-tapping screws and self-adjusting bolts of stainless steel for fixing the corrugated aluminum jackets on the tank body on the tank roof with hex head and neoprene washer, stainless steel bolts (welded on site) for fixing the smooth aluminum jacket on the roof tank with stainless steel nut and neoprene washer.
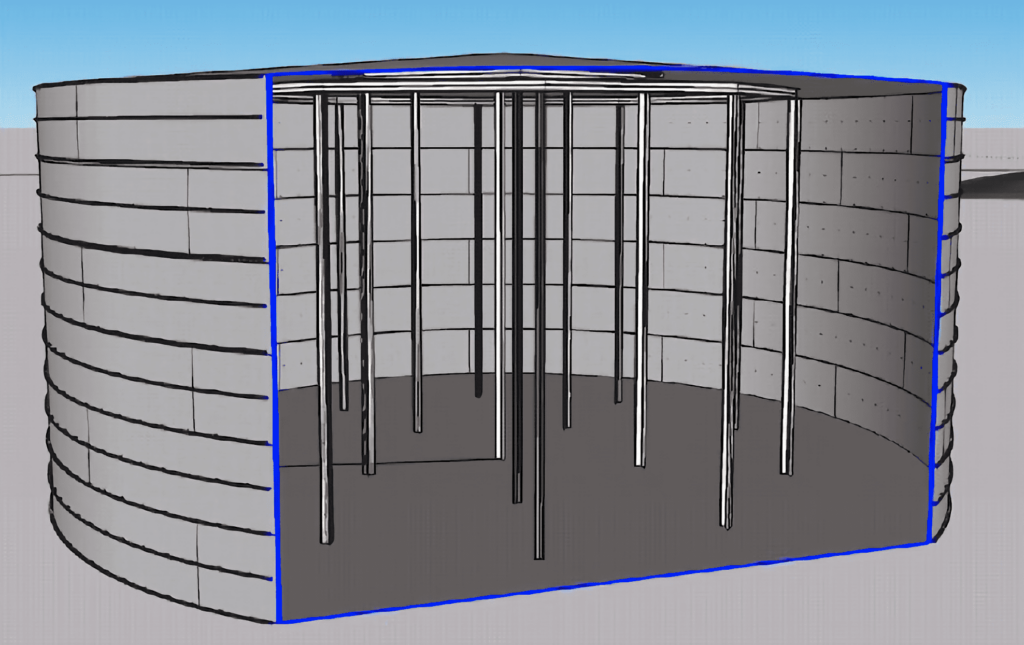
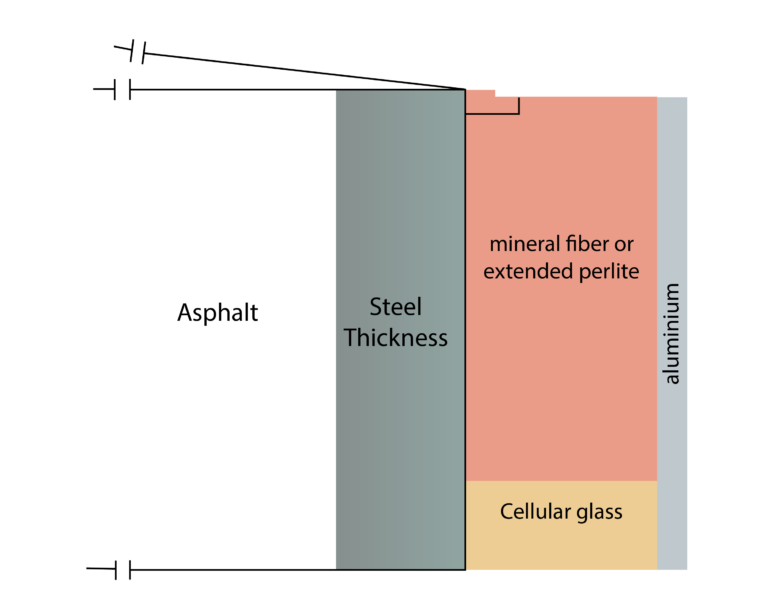
Asphalt Transportation(Liquid)
Liquid asphalt is normally transported by barge, asphalt tanker, tank truck or rail, from the refinery to the terminal, then it is pumped from the barge, ship, truck or train wagon to the storage tank, being channeled along supply pipe lines.
The asphalt arrives with a temperature between 300 and 325 ºF (148 – 163 °C) and is stored at the delivery temperature, since both the barges and the ships have heating coils using thermal oil, the train wagons have coils in their lower part of the wagon to keep it adequately warm.
At the destination, the asphalt is pumped into tanker trucks for distribution. These tankers are equipped with a thermal insulation system that allows the temperature of the asphalt to be maintained until its final delivery to the customer.
The following figure schematizes the transport of liquid asphalt.
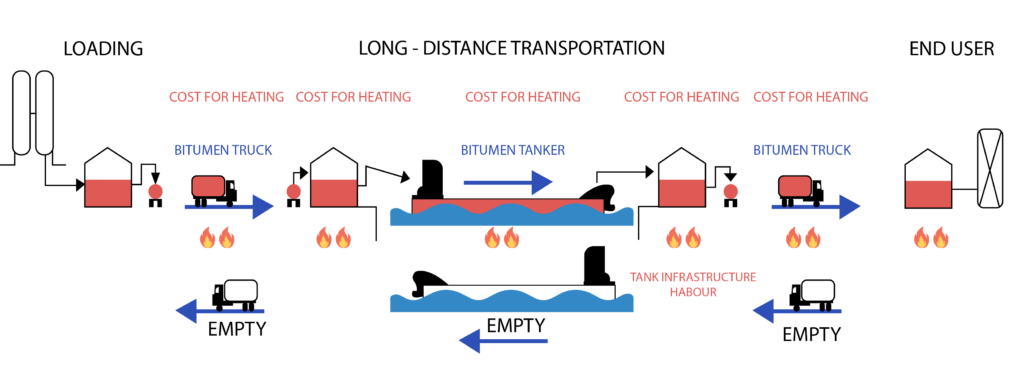
Asphalt Transport(Solid)
The compaction system for solid or cold asphalt is designed to pack asphalt for road paving in bags or flexible containers for cold asphalt, to be transported by any means of land transport. At the end of the supply chain is the fusion terminal, which consists of a small plant of a storage yard and a high-performance fusion unit, to re-melt cold asphalt, to be loaded onto tanker trucks, and transport it to the end customer or final use.
System advantage
The cold asphalt can be transported in ecological, flexible and light containers
The elements of the supply chain are:
The cooling and packaging unit: It is the first step in the supply chain of the asphalt compaction system. It consists of a small process plant, designed to be installed on a site close to or within the refinery. This unit can be fed (supplied) through pipes or through tanker trucks, where the liquid and hot asphalt is cooled to the packaging temperature for a stable, safe and continuous operation, to be later packed in bags for asphalt. The cooling and packaging unit operates semi-automatically and is electronically controlled to fill, individually weigh each bag and register each bag with a unique serial number and barcode.
The bag for asphalt; It is a flexible, self-stabilizing bag with UV protection, which allows the storage and transport of cold asphalt. This bag is designed to support a gross weight of up to 1,300 kg. Made of plastic material, composed of a multilayer outer bag (recyclable) and a special-purpose inner film, designed to be transported by any common transport system (container, truck , railway). It comes in different sizes to suit the requirements of the clients. Its shape and volume are optimized for maximum utilization of containers and trucks. The coating melts together with the asphalt without changing its quality properties. It includes a simple frame structure for additional stabilization to accommodate the larger mass.
Storage: Bags can be stored in cold conditions in any climate. The only requirement is a flat, compacted surface. It is suitable for all climate zones as they are protected against UV rays and can be stored for up to 12 months outdoors. However, for a long storage period, it is recommended to cover them or keep them under a roof to avoid direct sunlight.
Fusion terminals; they cover the “last step” of the supply chain, function as asphalt terminals and as storage space or facilities, where the asphalt must be re-liquefied for its final application. This is achieved by the high-performance fusing unit that is the core element of a fusing terminal.

General characteristics of a ship of asphalt
Asphalt ship tankers are in the group of the same name as chemical tankers, which transport IMO Class 9 products. These ships have a series of technical characteristics that do not vary since they are very typical of this type of oil tanker.
The first characteristic of asphalt tankers is that they must have “screw pumps” as exclusive pumps for unloading asphalt. These pumps are designed to pump high viscosity and high temperature products. They are a type of electric pumps, which work by amperage and, depending on the revolutions per minute that it rotates, will achieve a higher or lower discharge rate.
Another main characteristic is that they must have a heating system which must be made up of steam boilers to circulate the thermal oil through the ship’s pressure/return lines and heating coils, which are pipes through which it will circulate the thermal oil to the cargo tanks to keep the asphalt at the temperature with which it was loaded. The temperature of the asphalt is usually between 140 – 160 ºC.
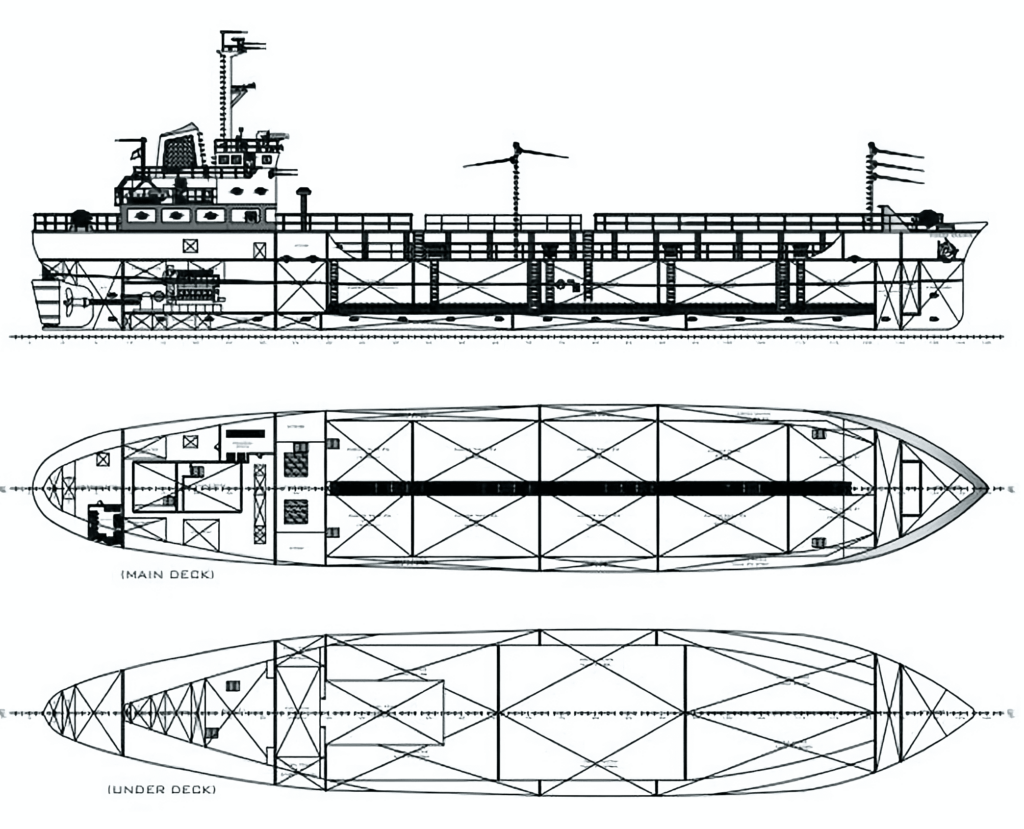